Jargon Busting: Understanding Health & Safety Terminology for Employees
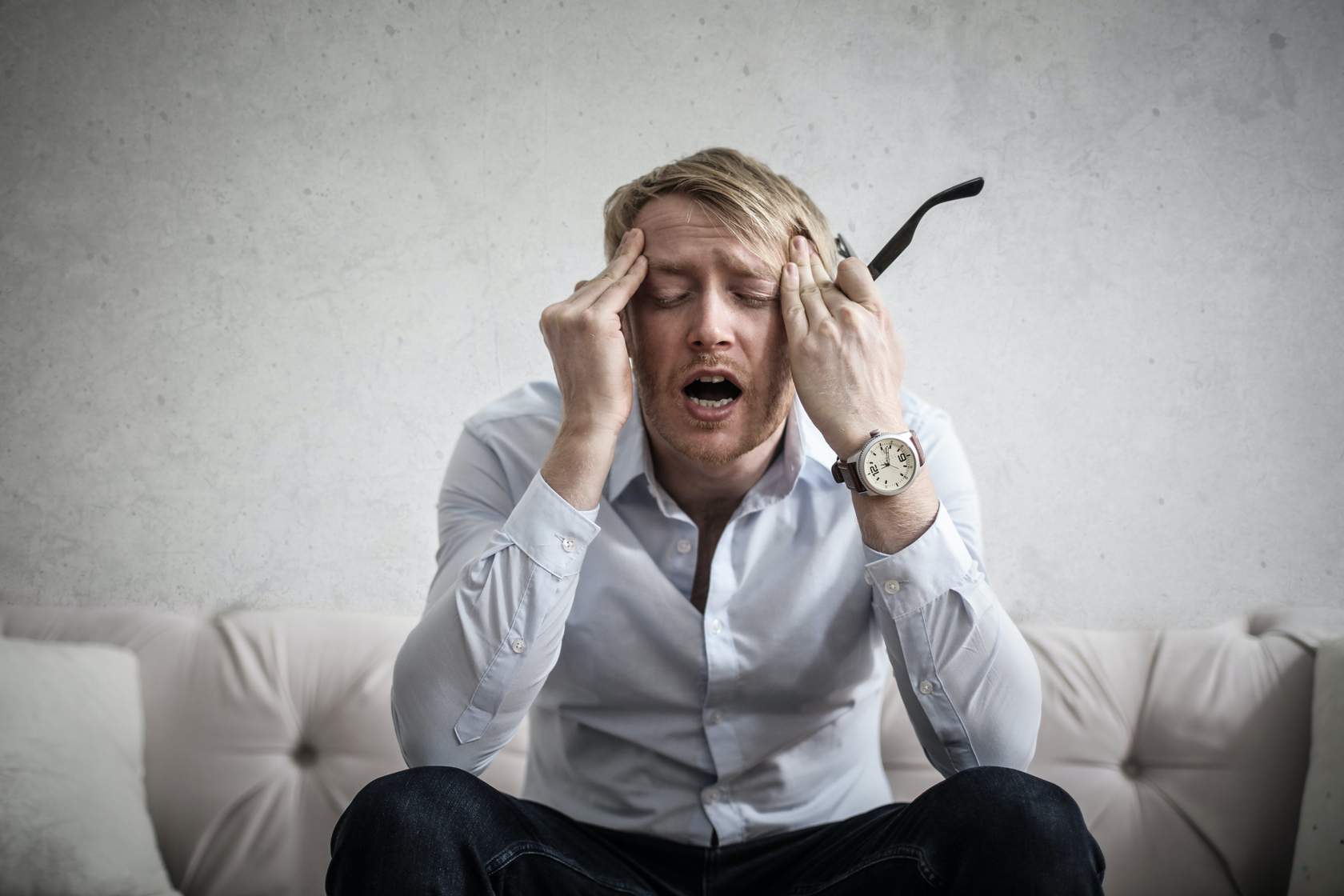
Navigating the world of Health & Safety Terminology can often feel like decoding a secret language. The field is rife with acronyms and jargon that can be confusing, especially for new employees. This blog aims to demystify some of the most common health and safety terms, making them more accessible and understandable for everyone in the workplace.
Incident vs. Accident vs. Near Miss: What’s the Difference?
Incident: An incident is an event that has the potential to cause harm or damage. This term is broad and encompasses both accidents and near misses. It’s important to report and investigate incidents to prevent future occurrences.
Accident: This is a specific type of incident that results in injury, illness, or property damage. Accidents are unplanned and unwanted events that are a clear indication of a break in safety protocol.
Near Miss: A near miss is an incident that could have caused harm but didn’t. This is a warning sign and a crucial opportunity for learning and prevention. Reporting near misses helps in identifying and mitigating risks before they lead to actual harm.
Planning for Safety: JHA, JSA, and JST
JHA (Job Hazard Analysis): This is a technique that focuses on job tasks to identify hazards before they occur. It involves breaking down a job into smaller tasks and analyzing potential risks associated with each step.
JSA (Job Safety Analysis): Similar to JHA, JSA is a process that helps identify dangers associated with a specific job or process. The goal is to reduce the risk of injury to workers.
JST (Job Safety Training): JST refers to the training provided to employees to perform their jobs safely. It encompasses both the identification of hazards and the measures to mitigate them.
Reporting and Compliance
RIDDOR (UK) (Reporting of Injuries, Diseases and Dangerous Occurrences Regulations) is specific to the UK. It mandates the reporting of:
- Work-related accidents causing death or certain serious injuries.
- Occupational diseases.
- Certain ‘dangerous occurrences’ (incidents with potential to cause harm).
- Gas incidents.
RIDDOR is enforced by the Health and Safety Executive (HSE) and sets specific criteria for reporting, including timelines and the level of detail required.
OSHA (USA) – In the United States, OSHA (Occupational Safety and Health Administration) oversees workplace safety. Unlike RIDDOR, OSHA has a broader scope and is not limited to specific incidents. Key aspects include:
- Reporting severe work-related injuries, including hospitalizations, amputations, or loss of an eye.
- Keeping records of work-related injuries and illnesses (OSHA 300 Log).
- Emphasis on employer’s responsibility to provide a safe workplace.
OSHA’s approach is less prescriptive in terms of specific incidents compared to RIDDOR but maintains a strong emphasis on employer responsibility and ongoing record-keeping.
HSA – Ireland’s Health and Safety Authority- Ireland’s approach, overseen by the Health and Safety Authority (HSA), is similar to RIDDOR. It includes:
- Reporting of fatal and non-fatal injuries.
- Reporting of occupational diseases.
- Reporting of certain dangerous occurrences.
Ireland’s system aligns closely with EU directives, focusing on both immediate incident reporting and ongoing health surveillance in workplaces.
EU Framework – The EU’s approach to workplace safety and health reporting is more a framework than a specific set of regulations like RIDDOR or OSHA. It establishes minimum requirements, and member states implement these through their own legislation (like RIDDOR in the UK and HSA regulations in Ireland). Key elements include:
- Reporting serious accidents and fatalities.
- Monitoring and reporting occupational diseases.
- Emphasis on prevention and risk assessment.
Acronyms explained
COSHH (Control of Substances Hazardous to Health)
COSHH is a UK-specific regulation requiring employers to control substances that are hazardous to health. It includes:
- Assessing risks posed by hazardous substances.
- Implementing measures to control exposure.
- Ensuring that control measures are used and maintained.
- Monitoring the effectiveness of control measures.
MSDS (Material Safety Data Sheet)
MSDS, or Safety Data Sheet (SDS), is a document that provides detailed information about a chemical substance or mixture. Key aspects include:
- Hazard identification.
- Composition/information on ingredients.
- First-aid measures.
- Fire-fighting measures.
- Accidental release measures.
PPE (Personal Protective Equipment)
PPE refers to protective clothing, helmets, goggles, or other garments or equipment designed to protect the wearer’s body from injury or infection. It’s critical for:
- Minimizing exposure to hazards.
- Protecting against workplace risks.
- Complementing other safety measures.
DSE (Display Screen Equipment)
DSE relates to any work equipment with a screen that displays information, commonly computers. DSE assessments are vital for:
- Reducing the risk of eye strain, fatigue, and musculoskeletal disorders.
- Ensuring that workstations are ergonomically set up.
- Complying with health and safety regulations regarding screen-based work.
LOTO (Lockout/Tagout)
LOTO stands for Lockout/Tagout and is a safety procedure used in industry and research settings to ensure that dangerous machines are properly shut off and not started up again before the completion of maintenance or repair work. It includes:
- Isolating energy sources.
- Applying locks and tags to prevent unexpected startup.
- Protecting workers from residual or stored energy.
Phrases and terms
Ergonomics
Ergonomics refers to the study of people’s efficiency in their working environment. It involves:
- Designing workplaces and job tasks for comfort, efficiency, and safety.
- Reducing the risk of musculoskeletal disorders.
- Improving productivity and worker well-being.
Hierarchy of Control
The Hierarchy of Control is a system used in industry to minimize or eliminate exposure to hazards. It includes:
- Elimination: Physically removing the hazard.
- Substitution: Replacing the hazard.
- Engineering Controls: Isolating people from the hazard.
- Administrative Controls: Changing the way people work.
- PPE: Protecting the worker with personal protective equipment.
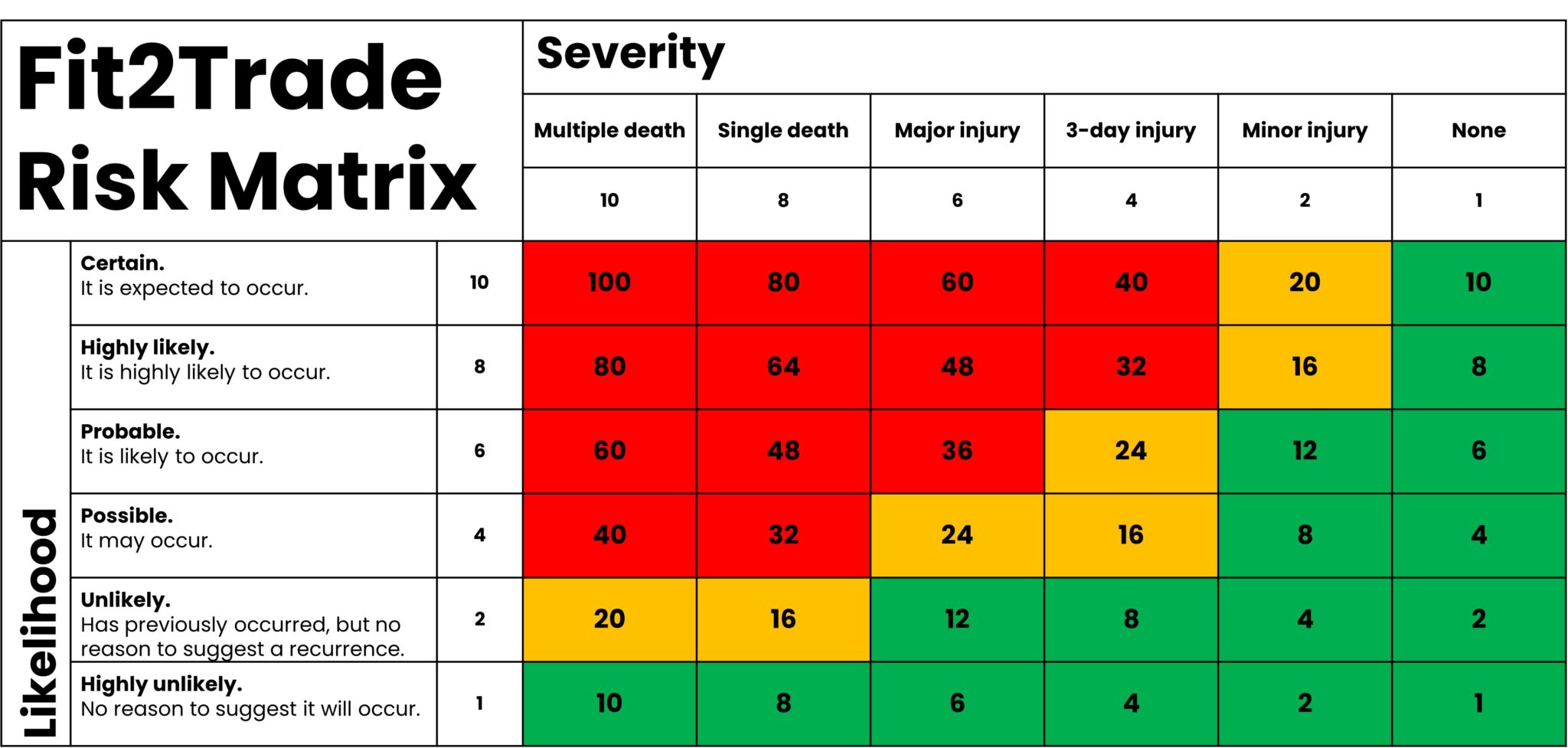
Understanding Risk Assessments
Risk Assessment
Risk Assessment is the process of identifying potential hazards in the workplace, evaluating the risks associated with them, and implementing measures to control or eliminate those risks. It involves:
Identifying Hazards: Recognizing anything that may cause harm, such as chemicals, work processes, or even certain work practices.
Evaluating Risks: Determining the likelihood of harm occurring and the severity of its potential impact.
Implementing Controls: Introducing measures to minimize or eliminate the risk.
Recording Findings: Documenting the hazards, their associated risks, and the measures taken to address them.
Reviewing and Updating: Regularly revisiting the risk assessment to ensure it remains relevant and effective, especially when there are changes in the workplace.
Primary Risk
Primary Risk refers to the initial level of risk associated with a hazard before any control measures are applied. It represents the inherent danger in a situation or activity. Understanding primary risk is essential for determining the necessary level of intervention and control measures.
Residual Risk
Residual Risk is the level of risk that remains after control measures have been implemented. No matter how effective controls are, there is often some level of risk that cannot be completely eliminated. Residual risk assessment is important to ensure that the remaining risk level is acceptable and does not pose a significant threat to health and safety.
Risk Matrix
A Risk Matrix is a tool used in risk assessment to help evaluate and prioritize risks. It typically involves:
Severity: Estimating the potential impact or consequences of a risk (e.g., minor injury, major injury, fatality).
Likelihood: Assessing the probability of the risk occurring (e.g., unlikely, possible, likely).
The matrix is a grid with likelihood on one axis and severity on the other, creating a visual representation of risk levels. Risks are then plotted on the matrix, helping to prioritize them based on their severity and likelihood. The resulting categorization (e.g., low, medium, high risk) guides decision-making about what controls should be implemented first.
At Fit2Trade, we demystify the complexities of health and safety regulations, making them accessible and understandable. We provide comprehensive training and resources that break down these concepts into easy-to-understand language and practical applications. Our approach ensures that employees are not just aware of the terms but understand their significance and how they apply to their daily work routines.
By partnering with Fit2Trade, businesses benefit from a knowledgeable workforce that is well-equipped to identify and manage risks effectively. This not only ensures compliance with legal standards but also fosters a safety-conscious culture within the organization. The result is a safer workplace, fewer accidents, and a more confident and productive team.
Remember, a safe workplace is a productive and happy workplace, and Fit2Trade is dedicated to helping you achieve just that. For more information and resources, visit us at Fit2Trade.com and take the first step towards simplifying safety in your workplace.
Written by Rory Byrne from Fit2Trade